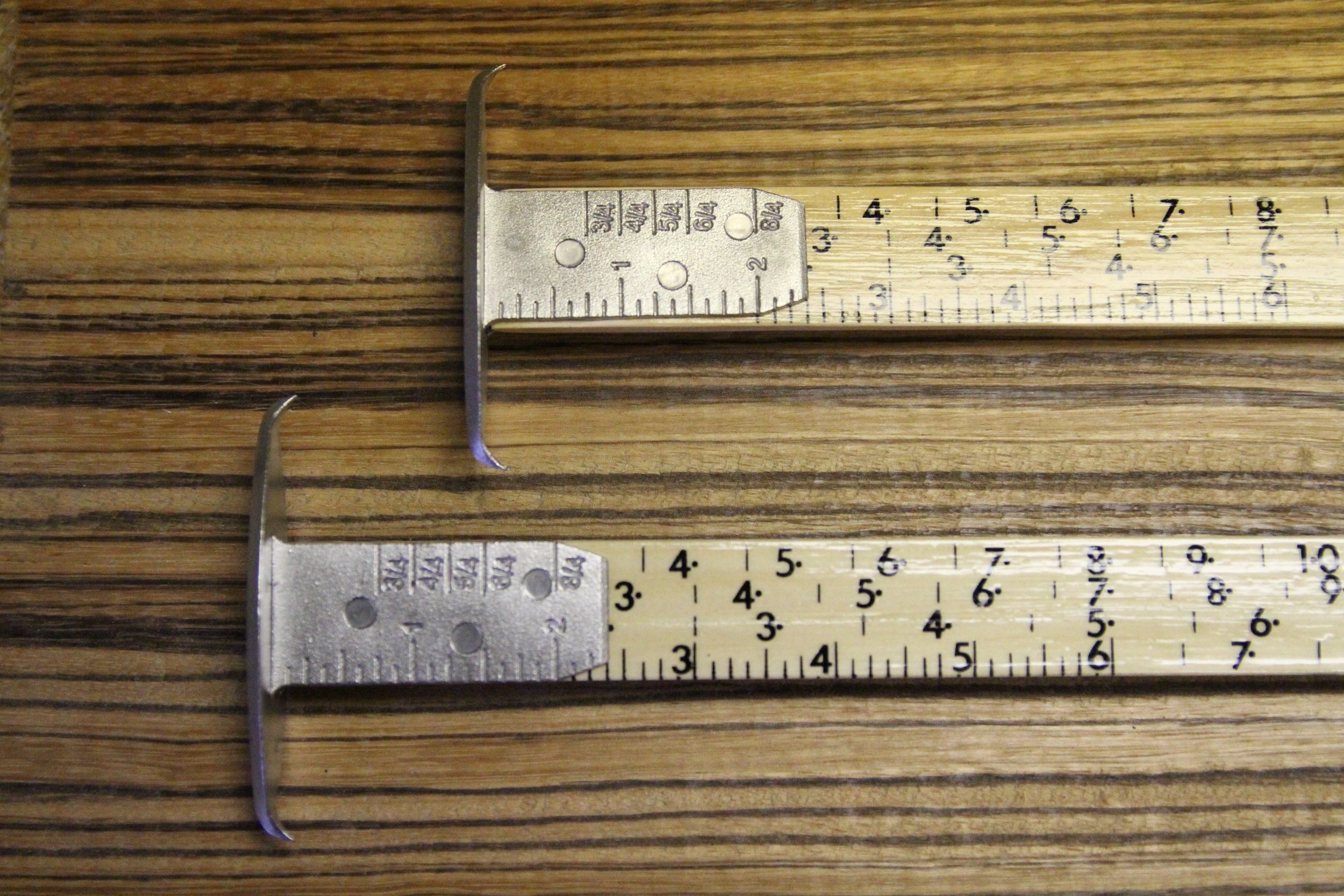
Understanding Hardwood Lumber Thickness: A Guide to Measurement
-
Nominal Thickness vs. Actual Thickness
Hardwood lumber is often sold with a nominal thickness, which is a rough estimate of its size. However, the actual thickness of the lumber can vary due to factors like drying and planing. When purchasing hardwood lumber, it's crucial to recognize the difference between nominal and actual thickness to ensure that it meets the project's requirements.
-
Rough Lumber Thickness
Hardwood lumber typically starts as rough lumber, which is the raw material obtained directly from the sawmill. The rough lumber's thickness is measured in quarters, with one quarter equal to 1/4 inch. For example, a 4/4 (pronounced "four-quarter") board has a rough thickness of approximately 1 inch. Similarly, a 8/4 board has a rough thickness of about 2 inches.
-
Drying and Surfacing
After the initial milling, hardwood lumber undergoes a drying process to reduce moisture content. This process helps prevent warping, cracking, and other issues. Once dried, the lumber is often surfaced, which involves planing to create a smoother and more consistent surface. This surfacing results in a reduction in the actual thickness of the lumber.
-
S2S and S4S Lumber
Surfaced lumber comes in two main categories: S2S (surfaced on two sides) and S4S (surfaced on four sides). S2S lumber is planed on the top and bottom surfaces, leaving the edges rough. On the other hand, S4S lumber is planed on all four sides, providing a smooth and uniform finish. When working with hardwood lumber, it's essential to consider whether S2S or S4S is suitable for the intended project.
-
Grading and Quality Control
Hardwood grading is a meticulous process essential for categorizing lumber based on quality, ensuring that consumers and woodworkers can make informed decisions tailored to their specific needs. Among the various classifications, Superior, FAS (Firsts and Seconds), Number 1, and Number 2 are key designations that denote the quality of hardwood lumber. Superior represents the pinnacle of grading, embodying wood of exceptional quality with minimal defects, uniformity in color, and a notable absence of knots. FAS, standing for Firsts and Seconds, is a premier grade that includes boards meeting stringent criteria for clarity and minimal imperfections. Within the FAS grade, there are further differentiations with Number 1, signifying an even higher standard of quality, and Number 2, providing an excellent balance between quality and cost-effectiveness. Each of these classifications plays a crucial role in meeting the diverse requirements of woodworking projects, allowing craftsmen to choose lumber that aligns precisely with their aesthetic preferences and functional demands. Understanding the nuances of these grades empowers woodworkers to create projects that not only meet but often exceed expectations in both appearance and structural integrity.
-
Kiln Dry vs Green (Wet) Hardwood
The choice between kiln-dried and green (wet) hardwood is a pivotal decision in woodworking, each option presenting distinct advantages and considerations. Kiln-dried hardwood undergoes a controlled drying process in a kiln, reducing its moisture content to a specific level. This method offers several benefits, such as enhanced dimensional stability, reduced risk of warping, and minimized susceptibility to insect infestation. The controlled environment of the kiln allows for a quicker drying time compared to air-drying methods, enabling woodworkers to work with more predictability. On the other hand, green or wet hardwood is freshly cut and retains a higher moisture content. While it may be more cost-effective initially, working with green hardwood requires careful consideration of potential shrinkage, warping, and the need for longer drying periods during the crafting process. The choice between kiln-dried and green hardwood ultimately depends on the specific requirements of a project, with kiln-dried wood offering a more stable and reliable material, particularly for fine woodworking where precision and stability are paramount.